Achievement of "stable and reliable product quality assurance" and "quick and accurate response"
Basic idea about quality
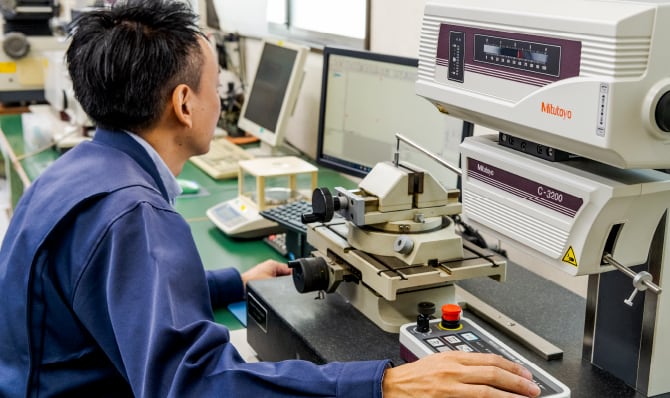
The products manufactured by Arai Parts are used in various areas of our daily lives, including automobiles.
We consider quality to be "stable and reliable product quality assurance" and "quick and accurate response", and we strive to continuously improve quality, such as acquiring quality management system certification and implementing substantial quality control process.
Quality policy and company slogan
- Quality policy
-
- Aim to further improve the quality level by continuous and consistent improvement.
- We aim to be a company that is trusted by our customers through reporting, contacting, and consultation.
- Company slogan
- Thoroughly review the procedure manual and standard. Check the product appearance thoroughly to reduce nonconforming products.
Efforts to improve quality: Obtained certification for quality management system
Arai Parts acquired the certification of quality management system "ISO9001" in August 1999. Currently, it is acquired at all factories and locations in Japan.
We use this system as a tool for stabilizing and improving quality, and we are promoting activities aimed at improving the quality of all operations.
This ideology does not change at our international locations.
We are also actively working to build high standard quality assurance systems at our international locations, and have acquired ISO and IATF certifications at our location in China.
Standard | Registered office | Obtained date |
---|---|---|
ISO9001 |
|
Acquired in August 1999 |
Taicang Factory, China | Acquired in December 2005 | |
Nagoya Sales Office | Acquired in June 2008 |
Efforts for fulfilling quality control
Quality conference for new product launch
We hold a new product progress meeting for all new products in which the person in charge from each section (quality assurance, engineering, manufacturing, sales) participates.
We have established a system to carry out process design, incorporating past trials, and pointing out potential problems before the start of mass production.
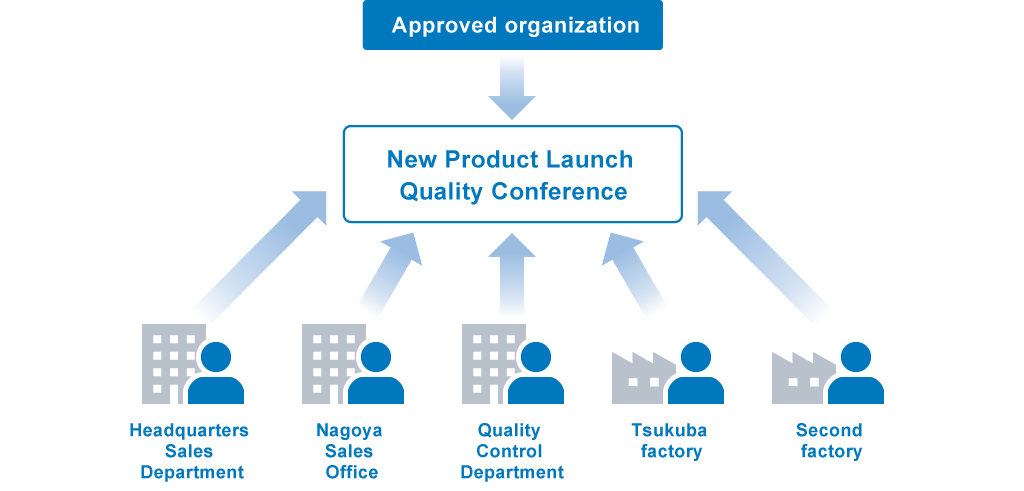
Thorough detection of NG products by visual inspection
We are focusing on early detection based on the idea that serious defects can be eradicated by finding anomalies and taking prompt action.
Workers use check sheets to check the manufacturing sites once a day, and two management departments carry out patrol checks twice a day.
If an abnormality is found, we immediately report it to the supervisor.
In addition, the daily closure meeting is used as an opportunity to listen to the workers' burden, dissatisfaction, etc., in an effort to improve working condition and efficiency.
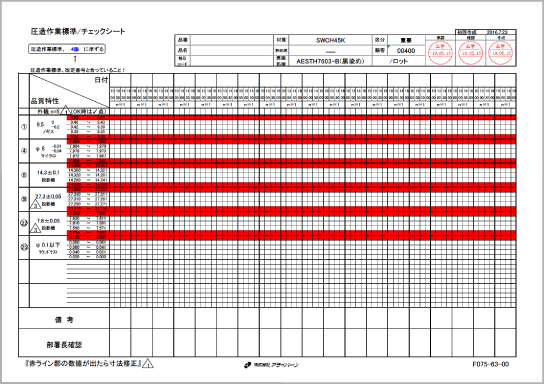
Check sheet
Shipment inspection by an in-house certified inspector
In-house certified inspectors carry out shipping inspections and guarantee products' quality.
Certified inspectors continue to participate in regular inspection study sessions to maintain and improve their abilities.
We have created a system that allows all inspectors to perform inspections with the same accuracy
The contents of the inspection standards exchanged with customers are registered and shared within the database.
It is possible to search the product numbers and look up the inspection items, inspection methods, and precautions during inspection, so that all inspectors can perform the same exact inspection at any time.
The inspection results are stored permanently in a database.
If a non-standard value is entered into the inspection device, the error will be displayed in red, so abnormality will not be missed.
Sharing of defect information using groupware
Defect information can be shared with photos on groupware that can be viewed on all terminals within the company, and can be checked by relative departments at the same time.
We have also built a system that enables quick initial response to problems such as investigation of change points and probable causes.